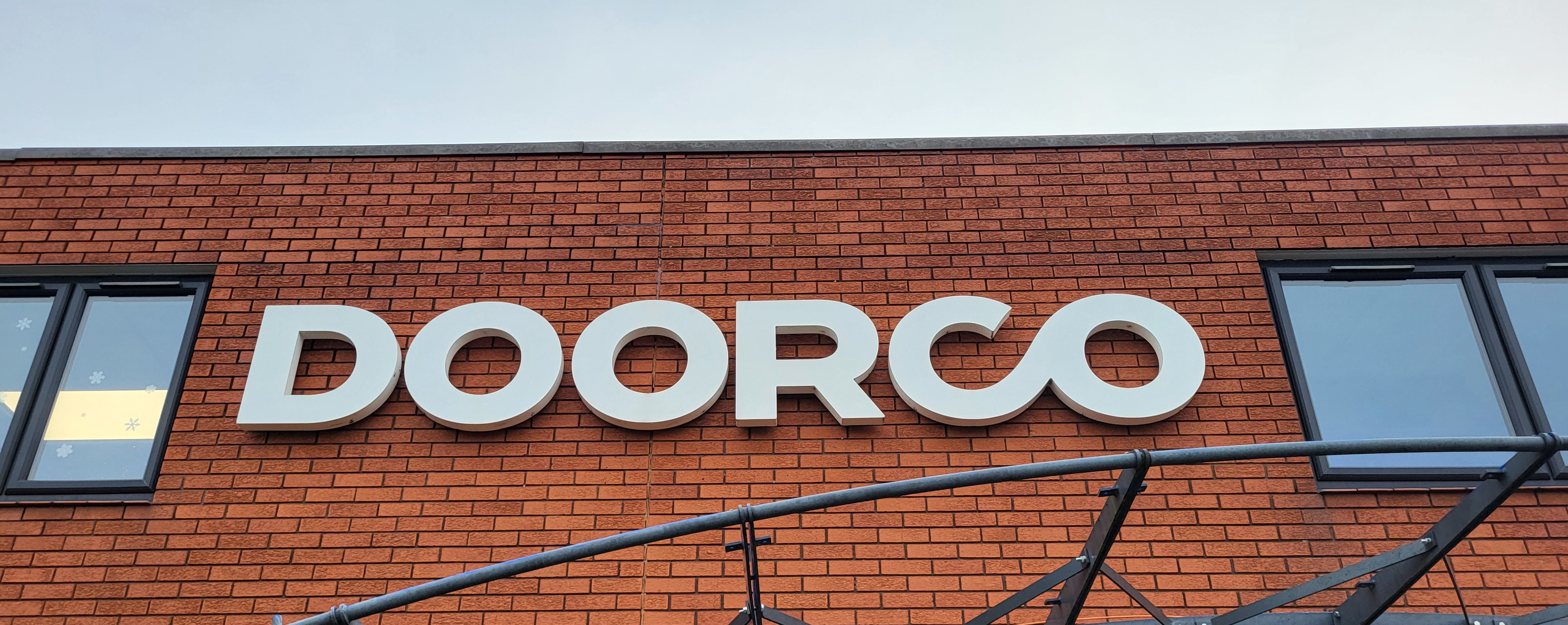
How DoorCo Improved Production by 26% with TrackMyMachines
Monday Dec 09, 2024
We interview Chris Mansfield, Senior Manufacturing Manager at DoorCo Ltd, who explains how TrackMyMachines has shifted the production culture at their Macclesfield Site.
About DoorCo
DoorCo is a global leader in composite door manufacturing, celebrated for its sustainable and thermally efficient doors. With over 3,750,000 units supplied worldwide to date, the company is committed to delivering high-quality products whilst pursuing innovation in its manufacturing processes.
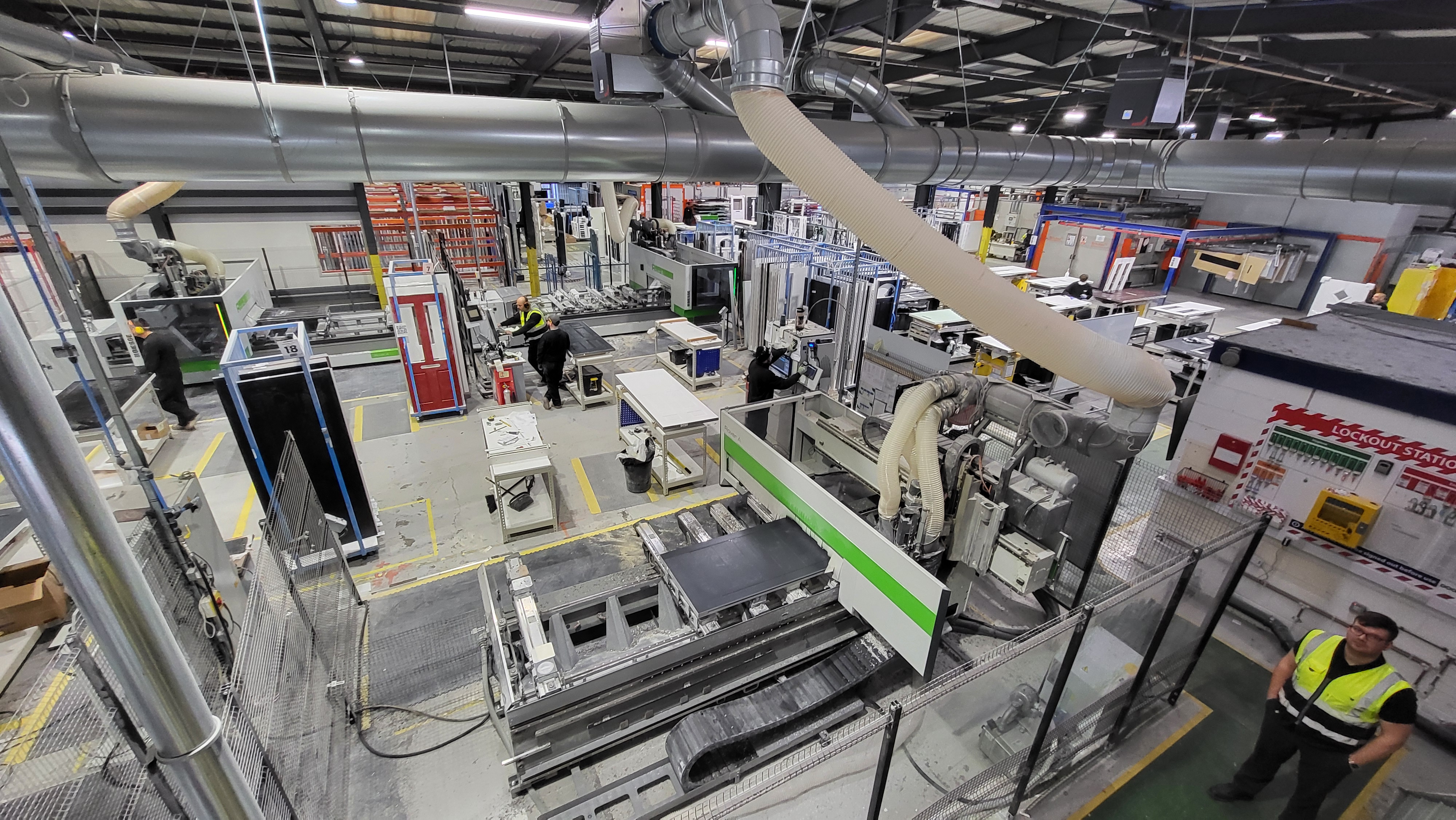
The Challenge
Meeting increasing customer demand without compromising efficiency is a common challenge for manufacturers. At DoorCo, Chris Mansfield, Senior Manufacturing Manager, highlighted how inefficiencies in tracking production and downtime led to difficulties in maximising machine performance.
We needed a way to identify bottlenecks and inefficiencies quickly without disrupting operations. Our goal was to remain agile and efficient as demand grew.
Previously, production planning relied on estimated metrics, such as predicting the number of doors each machine could produce daily. However, variations in door styles and complexities of process flow meant these estimates were inaccurate and the actual factory capacity was unknown and therefore under-utilised.
The Solution: TrackMyMachines
DoorCo partnered with TrackMyMachines to implement a real-time CNC machine monitoring solution. The system is now integrated into daily operations.
“Every CNC operator has it on their tablets. All the production managers have it. Even Aaron, our Operations Director, is checking it daily,” says Chris.
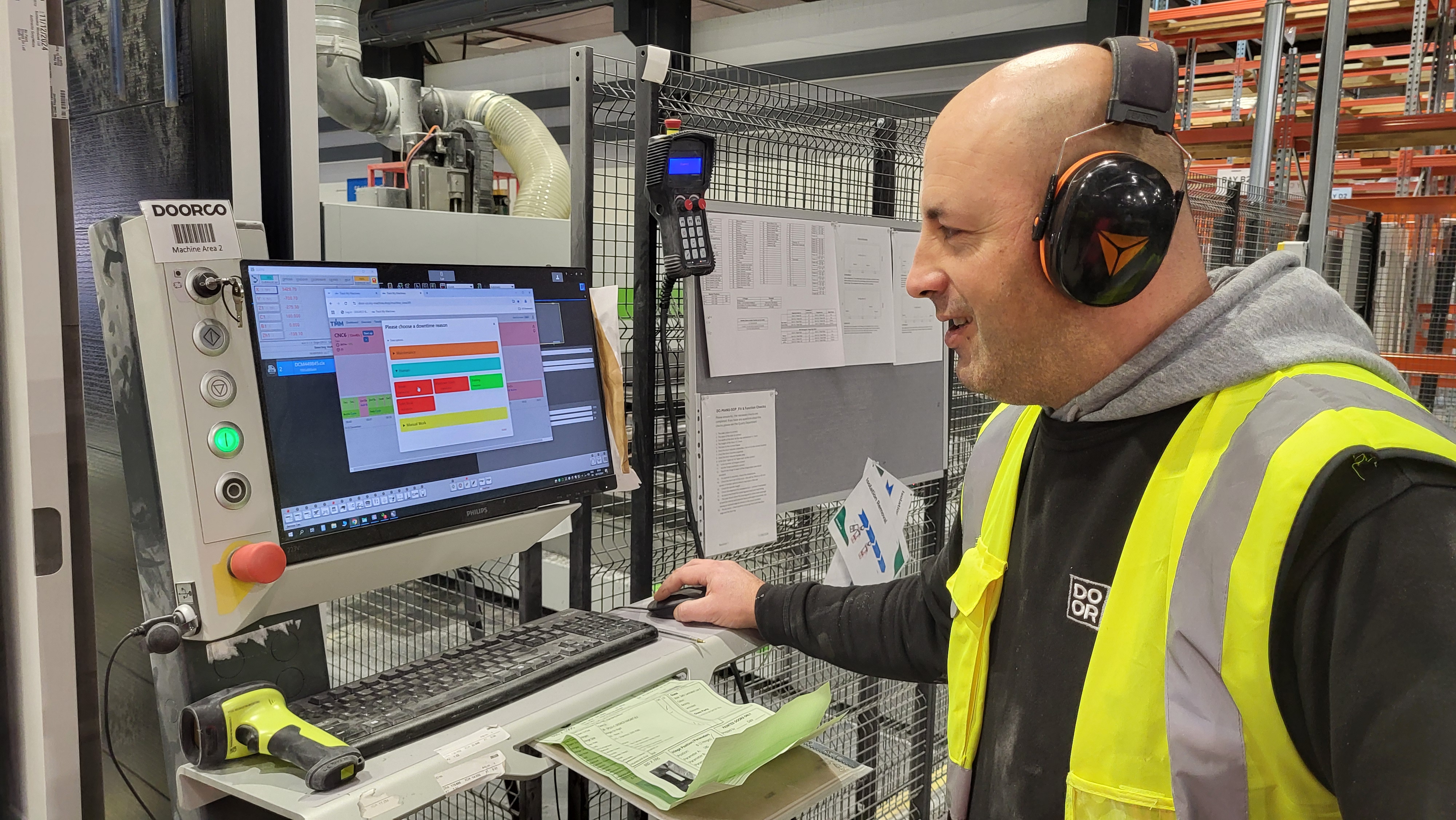
Key TrackMyMachines features utilized by DoorCo include:
- Real-Time CNC Machine Monitoring: Quick visibility into whether machines were operational and productive via a simple red/green system.
- Downtime Tracking: Identifying and categorizing downtime events to address recurring issues.
- Customizable Reporting: Easy generation of reports for downtime analysis and uptime tracking.
“The reports are straightforward and easy to use. No matter who we’ve trained, they pick it up quickly,” Chris noted.
The Results: 26% increase in production rates
After using TrackMyMachines to help with management changes, DoorCo have seen an uplift in production by almost 26%.
We've moved from 230 units per day to 340 units per day over the past year. Taking into account a new machine which added 50 units per day by itself, we've seen an extra 60 units per day just from tracking and pushing our production harder.
The Cultural Shift: From Units to Hours
One of the most significant changes brought about by TrackMyMachines was a shift in how they planned production.
“It’s taken us from chasing units to chasing hours,” Chris explained. “In manufacturing, people often focus on pushing units out the door. Instead, we now prioritize minimizing downtime and maximizing machine hours. If all our machines run 9 hours out of 11, the units will naturally follow.”
This cultural shift empowered the team to focus on what truly matter for long-term efficiency: operational uptime.
Chris described the process, “So that’s exactly why this is really beneficial for us, because what we used to do is we used to plan for a predicted amount off each machine. so we would say we want 60 doors per day off each machine but ultimately we know that if we run in a certain style of door we can get more than that. If we run what about five doors or something like that, which is a little bit more intricate, we’re going to get less. Whereas now we’re tracking it in hours, we just want to make sure the machine is running to its maximum capacity. it makes planning so much simpler.”
Downtime Reasons captured from day 1
As part of the implementation, Manufacturing Cell Manager Abbie Lever was tasked with making sure downtime reasons were captured effectively by the whole production team. Without requiring training, she took the task head-on.
“It’s such a simple interface, I didn’t need any training to get started. I could set up the correct downtime reasons for our factory and make sure that they were being captured in a few days.”, Abbie explained. She added that ” When it comes to analysis, the reporting is easy to use and fast to visualise what’s happened on the shop floor”
Results and Benefits
-
Improved planning: Real-time data on machine hours replaced the reliance on estimated cycle times. This made production scheduling more accurate, even for complex door styles.
“We used to predict six minutes per door, but variations meant this wasn’t reliable. Now, we focus on keeping machines running to capacity.” -
Simple but effective: The system’s simplicity encouraged widespread adoption among staff, regardless of technical expertise. “Our production managers aren’t tech-savvy, but they use it daily because it’s so intuitive.”
-
Actionable downtime tracking: Downtime tracking allowed DoorCo to identify and address recurring issues, from tool maintenance to process adjustments.
“If we notice consistent downtime for maintenance, we can dig into why and make changes.”
Looking Ahead
With the TrackMyMachines system now embedded into their operations, DoorCo is exploring ways to utilize the wealth of data generated. As Chris puts it:
“We’re now stable enough to use the system to its full potential. The next step is analyzing the data for broader efficiency gains.”
By embracing real-time monitoring and shifting their operational focus, DoorCo exemplifies how door manufacturers can leverage data-driven insights to improve productivity and foster innovation.
“Hopefully we’ll be rolling out to other sites in the new year.”
This transformation reflects not just a technical upgrade but a shift in mindset—one that prioritizes efficiency, sustainability, and growth.