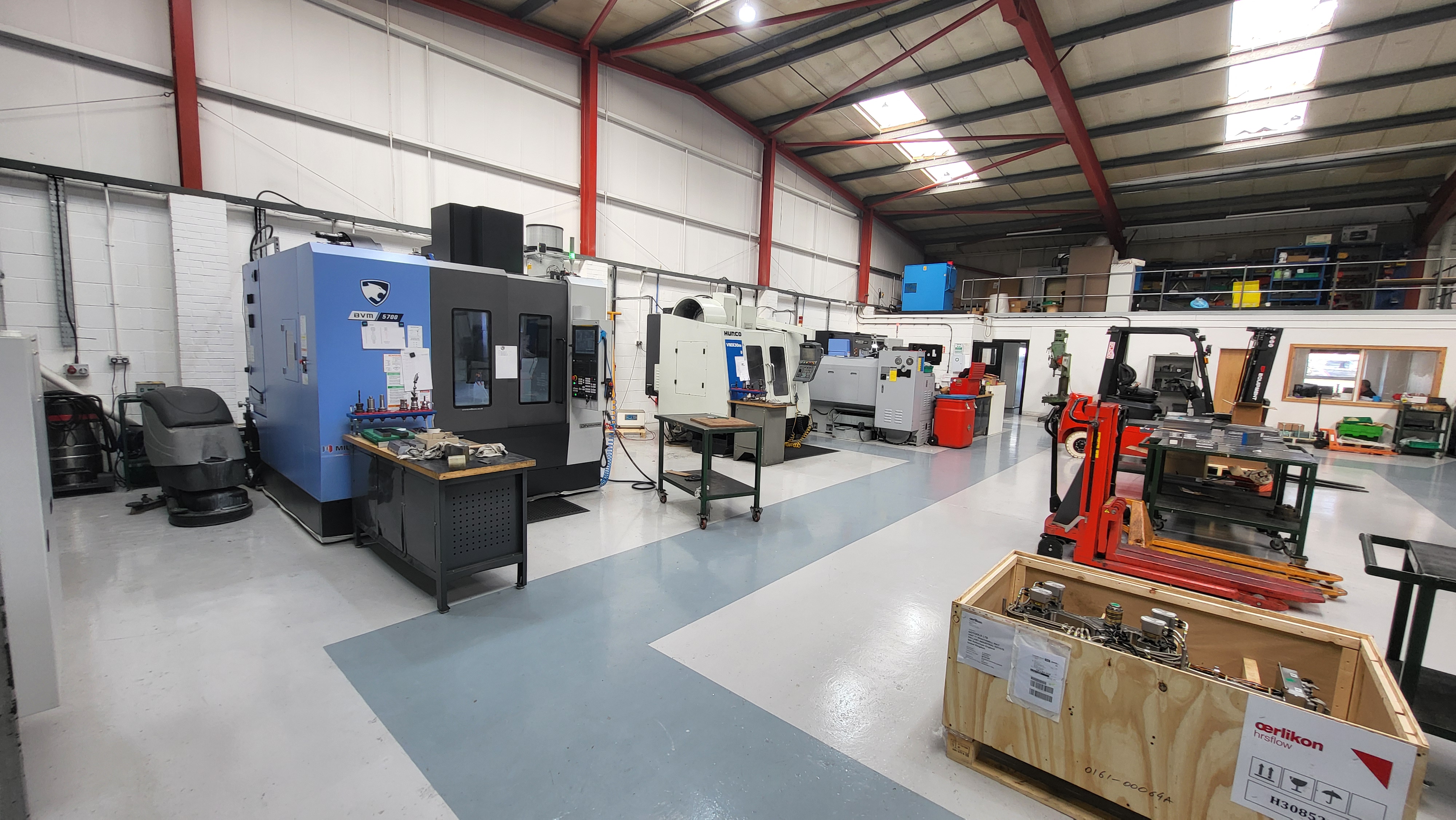
The Hidden Cost of Long Lead Times on Your Shop Floor
Monday Apr 07, 2025
If your machines only make parts when someone’s watching them, you’re leaving money on the table.
Long lead times aren’t just an inconvenience—they’re a red flag. They point to underutilised equipment, inefficient processes, and missed opportunities. If your production schedule depends on who’s available rather than what’s possible, it’s time to rethink how your shop floor works.
Lights-out manufacturing means your machines keep producing after the last person clocks out. It means turning evenings, weekends, and downtime into throughput—without hiring more people or working longer hours. And it might be the easiest way to cut lead times without cutting corners.
Lead Times: More Than Just a Number
Lead time is simple: it’s the span from when a customer places an order to when they get their parts.
Short lead times are preferred by almost everyone in the business and outside it, from your accountants to your customers. The earlier an order can be invoiced, the better.
But long lead times have complex effects. They slow down cashflow, frustrate returning customers, and can cost you the next order. Buyers are increasingly choosing suppliers who deliver quickly—and reliably. If your delivery is two weeks slower than the next shop’s, your quote might not even get read.
The Real Cost of Sticking to Day Shift-Only Work
If your shop’s only productive 8 hours a day when someone’s attending it, you’re using a third of your available capacity. That’s a problem.
Especially as UK labour costs climb, every minute of your engineering team’s time counts more than ever.
Most machines sit idle through:
- Evenings and weekends
- Lunch breaks and shift changeovers
- Setups and first-article inspections
- Delays while waiting for someone to notice and fix a problem
You paid for 24/7-capable machines. Why only use them a third of the time?
Compare a shop running 8 hours a day to one running 16+ via automation. Same headcount. Same machines. Double the throughput. That’s how you reduce lead times without buying a single new spindle.
Long-runners vs short-runners
Even without automated machinery that can change a component, if you’ve got long and short-running operations you can leave machines running after the end of the day for the rest of the cycle. Some engineers might balk at the idea of leaving a titanium roughing operation unattended, but how many of your jobs are actually simple finishing operations that don’t have a high risk of tool breakage?
One option is to rough components on the day-shift, then leave the long-running finishing operations to run overnight. Reducing the risk of a tool breakage.
What’s Slowing You Down?
Here’s what often gets in the way:
- No smart planning of operations during a day
- Long cycles that eat into shift hours
- Long setup times resulting from difficult workholding and tooling changeovers
- Operators reacting to problems instead of preventing them
All of these add up to machines sitting still when they could be making parts.
Using Monitoring and Automation to Shrink Lead Times
Automation
Your CNC machines are already automated. Once you hit cycle start, they don’t need help—until they do. The challenge is reducing the number of times they stop unexpectedly.
Start with your biggest sources of downtime. If you’re constantly changing over work, ask why. Is it because you’ve got the wrong person-machine ratio? Or because your fixtures aren’t repeatable enough? Solving these is a faster way to improve throughput than quoting for a new 5-axis.
Not every job is suited for full lights-out machining, but plenty of operations are. A simple finishing pass, a facing cut, or a long bore—these are exactly the kinds of cycles that could be running at 3am.
And it doesn’t take full automation to get started. Just make sure your existing machines are doing something when the lights go out.
Monitoring
Monitoring gives you the confidence to run lights-out—and the visibility to know what’s going wrong when it doesn’t work.
With machine monitoring you can:
- Track expected vs real button-to-button time, live
- Watch your changeovers reduce over time as your team gets better
- See when setups overrun or jobs stall
- Schedule smarter based on when your machines are actually free
- Get real-time alerts when a machine stops
- Let operators see how their shift compares to the last one
Most shops are still estimating utilisation. If you’re measuring it, you’re ahead. If you’re improving it, you’re winning.
When you can see the downtime reasons, you can fix them. When you can measure uptime shift-by-shift, you can schedule with intent. When you can spot the long-runners, you can choose the right jobs for overnight.
Running overnight shouldn’t feel risky. With the right data, it feels obvious.
Conclusion: Stop Limiting Your Throughput
If your machines only make parts when someone’s there to watch them, you’re voluntarily increasing your lead times.
Stop guessing. Start measuring. Your machines could be making parts right now—even if nobody’s there.