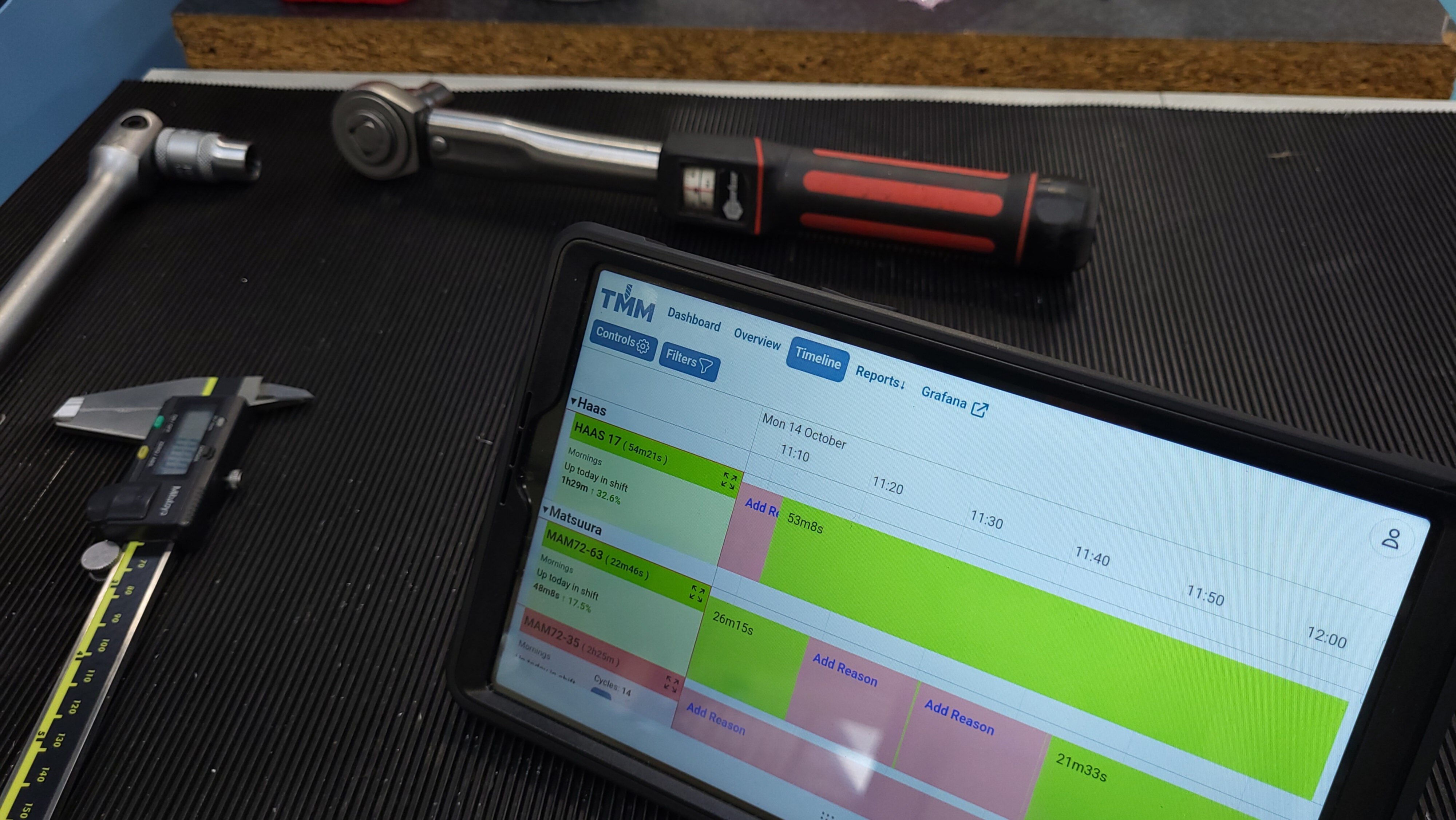
As a data-driven manufacturer, you’re always looking for ways to optimize efficiency and make informed decisions. One of the most common approaches we see in industry is Shop Floor Data Capture (SFDC)—a method for logging job operations, tracking production flow, and improving visibility on the shop floor.
Traditionally, SFDC relies on manual data entry, where operators log when a job starts and stops, moving work through the system. While this provides a structured way to track production, it has a major drawback—humans are flawed. Even in the best-run manufacturing environments, operators don’t always input data 100% of the time, leading to gaps, inaccuracies, and inefficiencies.
At TrackMyMachines we take our customers on a journey towards being more data-driven. We acknowledge your engineering team need to be doing the most important things first like producing components and maintaining machines, and collecting data last. That’s why we focus on automated data-collection through CNC machine monitoring before we start to introduce your company to capturing data like Downtime Reasons on the shop floor
In this article, we’ll explore the role of shop floor data capture, its limitations, and how automated CNC machine monitoring can drive better results in a modern, data-driven manufacturing shop.
Why Shop Floor Data Capture Matters
Despite not being 100% reliable, SFDC is still one of the most widely used methods for tracking job operations in CNC manufacturing. By logging when jobs start and stop, manufacturers gain better visibility into lead times, cycle times, and work-in-progress (WIP).
The Role of Data in CNC Manufacturing
In theory, a well-run SFDC system should allow you to:
- Track production flow and identify bottlenecks in the process
- Log accurately where components are in their route flow
- Log accurate setup and cycle times for your components
Logging the actual setup and cycle times is essential, as it allows for an evaluation of the true costs associated with each job. Once evaluated, the results can enhance the accuracy of future quotations and improve planning for similar jobs.
The Reality of Manual Data Entry
Despite its potential, traditional SFDC relies on operators manually inputting data, which introduces several challenges:
- Missed or delayed entries – Operators prioritize machining over data entry, leading to missing or inaccurate timestamps
- Human error – Typos, incorrect job selections, or rushed inputs makes this production data unreliable
- Lack of real-time insight – Data is only as good as what gets entered, meaning manufacturers often work with incomplete or outdated information
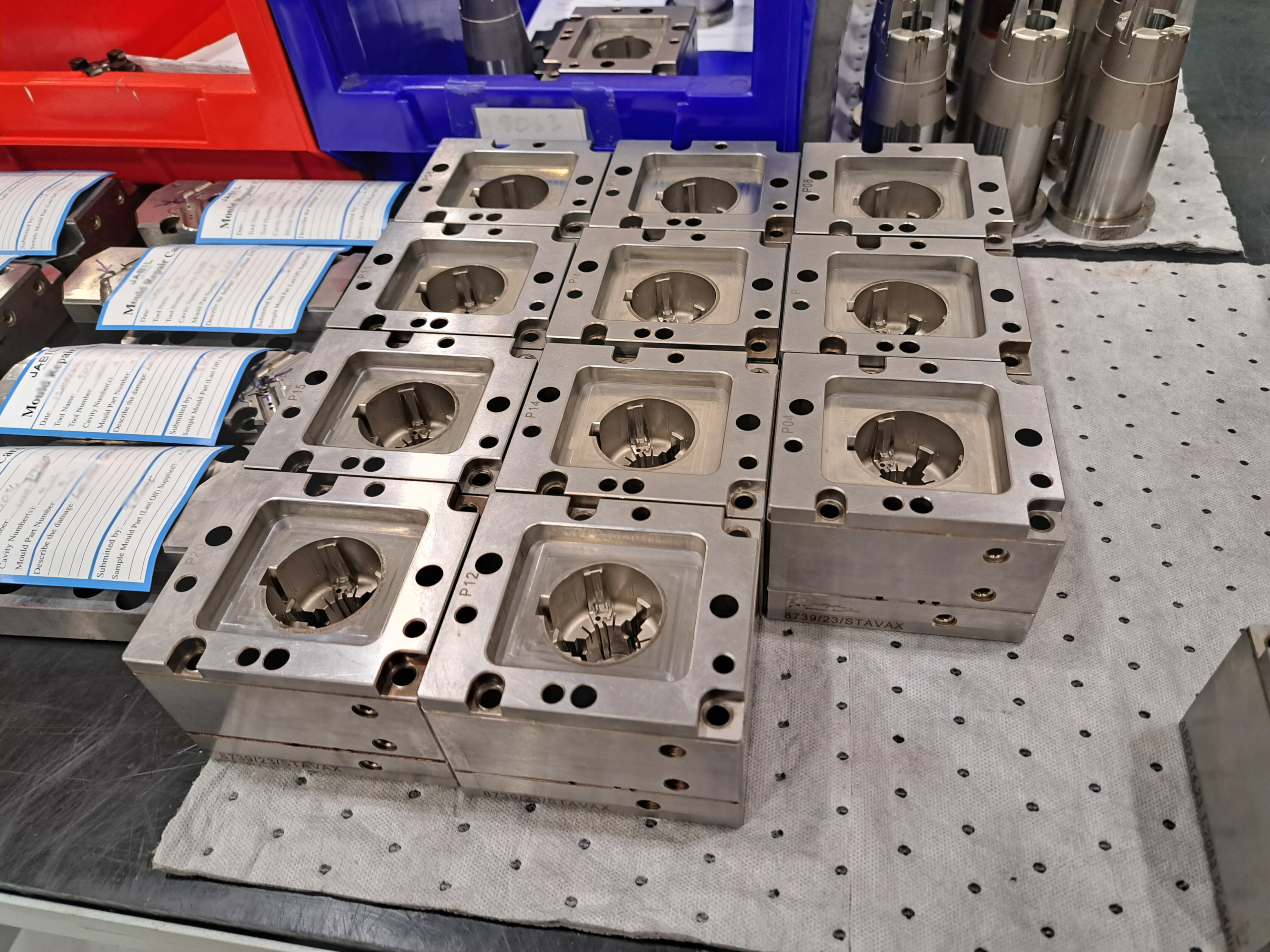
How many times have you finished a 50 off batch, then gone to the SFDC terminal to start and stop a job? It definitely didn’t just take 2 seconds to produce that batch, but that’s what you just told your production software.
For manufacturers looking to embrace data-driven manufacturing, these issues present a fundamental challenge: how do you ensure reliable, accurate, and real-time data capture without overloading operators with non value-add jobs?
That’s where automated CNC machine monitoring changes the game.
The Impact of Poor Data Collection
When shop floor data is incomplete or inaccurate, it creates a ripple effect across production planning, costing, and overall efficiency. Here’s how poor SFDC data can negatively impact a CNC manufacturing shop:
1. Inaccurate Job Costing & Quoting
Without accurate setup and cycle times, job costing becomes unreliable. If your estimated cycle time is 2 minutes per part but the actual time is 3 minutes, your shop is running at a 33% higher cost than planned—eroding your margins. Poor data means future quotes could be either too low (leading to lost profit) or too high (losing competitive bids).
2. Unreliable Production Scheduling
When SFDC data isn’t consistently logged, your production planner is making decisions based on incomplete or misleading information. Jobs may appear to be ahead of schedule when they’re actually behind, leading to last-minute scrambles, rushed setups, and missed delivery deadlines.
3. Increased Machine Downtime
Without real-time insight into spindle uptime, tool changes, and idle time, it’s impossible to proactively address inefficiencies. Machine monitoring solutions help identify hidden downtime—such as excessive setup time, waiting for materials, or unplanned stoppages—so you can take action before they impact your delivery targets.
4. Lack of Trust in Data-Driven Decisions
If engineers, operators, and managers don’t trust the data, they won’t use it. When manually logged SFDC data is frequently inaccurate, it leads to skepticism toward reports and dashboards. The result? Decisions are made based on gut feel rather than real data, limiting opportunities for continuous improvement.
The Shift to Automated & Real-Time CNC Machine Monitoring
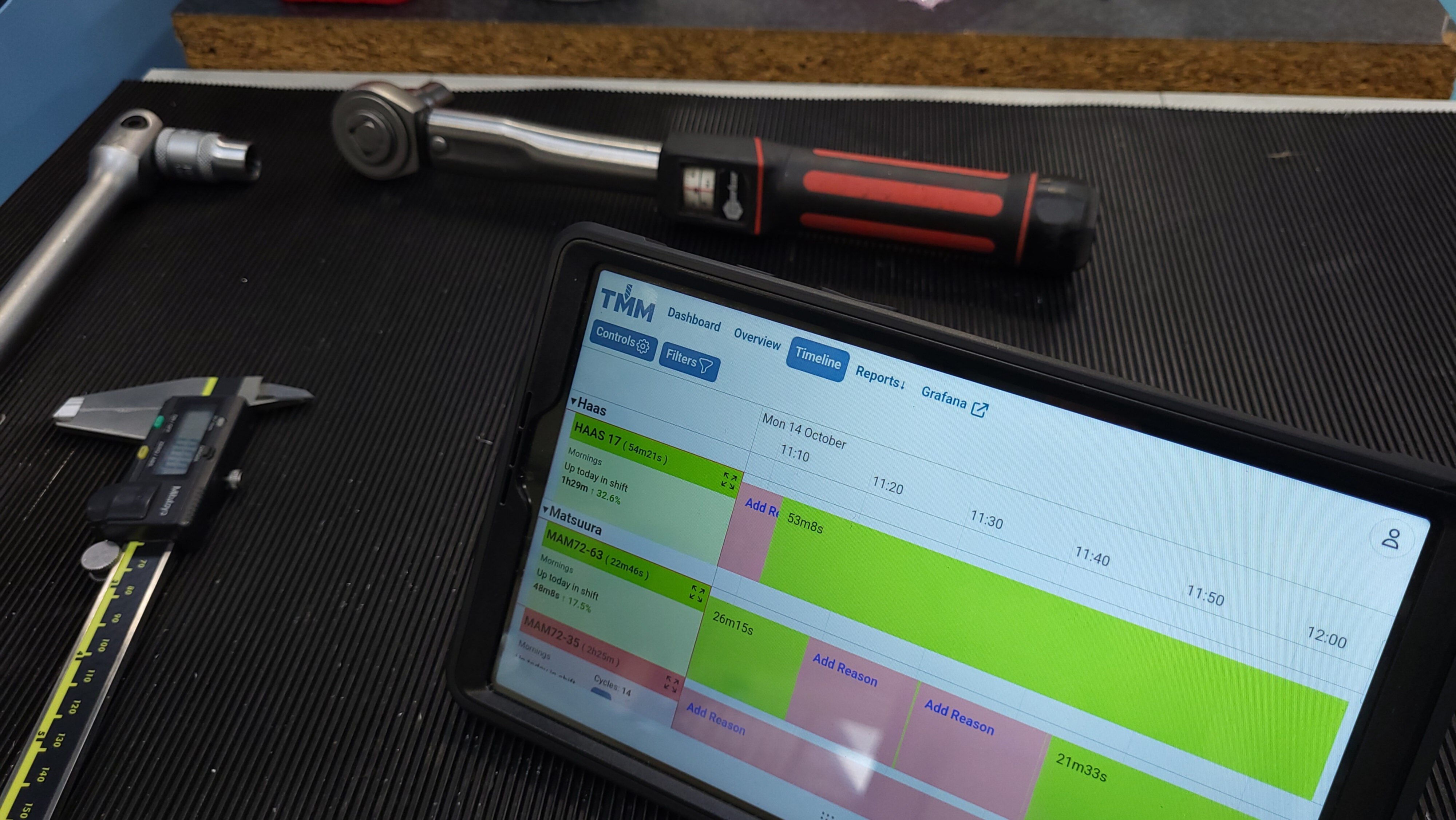
Relying on manual data entry for shop floor data capture is like using a stopwatch and notepad to track machine performance—it’s outdated, inconsistent, and prone to errors. Modern CNC shops are moving towards automated data collection, where real-time machine data is captured directly from the CNC control, eliminating the need for manual inputs.
How CNC Machine Monitoring Works
Automated CNC machine monitoring systems, like TrackMyMachines, capture data independently and, where possible, integrate directly with your CNC machines to:
- Capture real-time spindle activity – Know when a machine is running, idle, or stopped.
- Track cycle times automatically – No more relying on operators to remember to log start/stop times.
- Log feed rate overrides and spindle loads – Gain deeper insights into machine performance and efficiency.
The Benefits of Automated Data Capture
By replacing manual SFDC with automated CNC machine monitoring, manufacturers can:
- ✅ Eliminate human error – Data is logged automatically, ensuring accuracy and consistency.
- ✅ Gain real-time visibility – Know exactly what’s happening on the shop floor at any moment.
- ✅ Improve scheduling & job tracking – See live machine status and optimize job flow.
- ✅ Enhance job costing accuracy – Get precise cycle times to refine quoting and improve profitability.
- ✅ Identify hidden inefficiencies – Spot production bottlenecks and optimize machine utilization.
Bridging the Gap Between Manual & Automated Data Capture
At TrackMyMachines, we recognize that transitioning from traditional SFDC to fully automated machine monitoring is a journey. That’s why we help manufacturers start with real-time CNC machine data before layering on manual data points like Downtime Reasons and operator feedback.