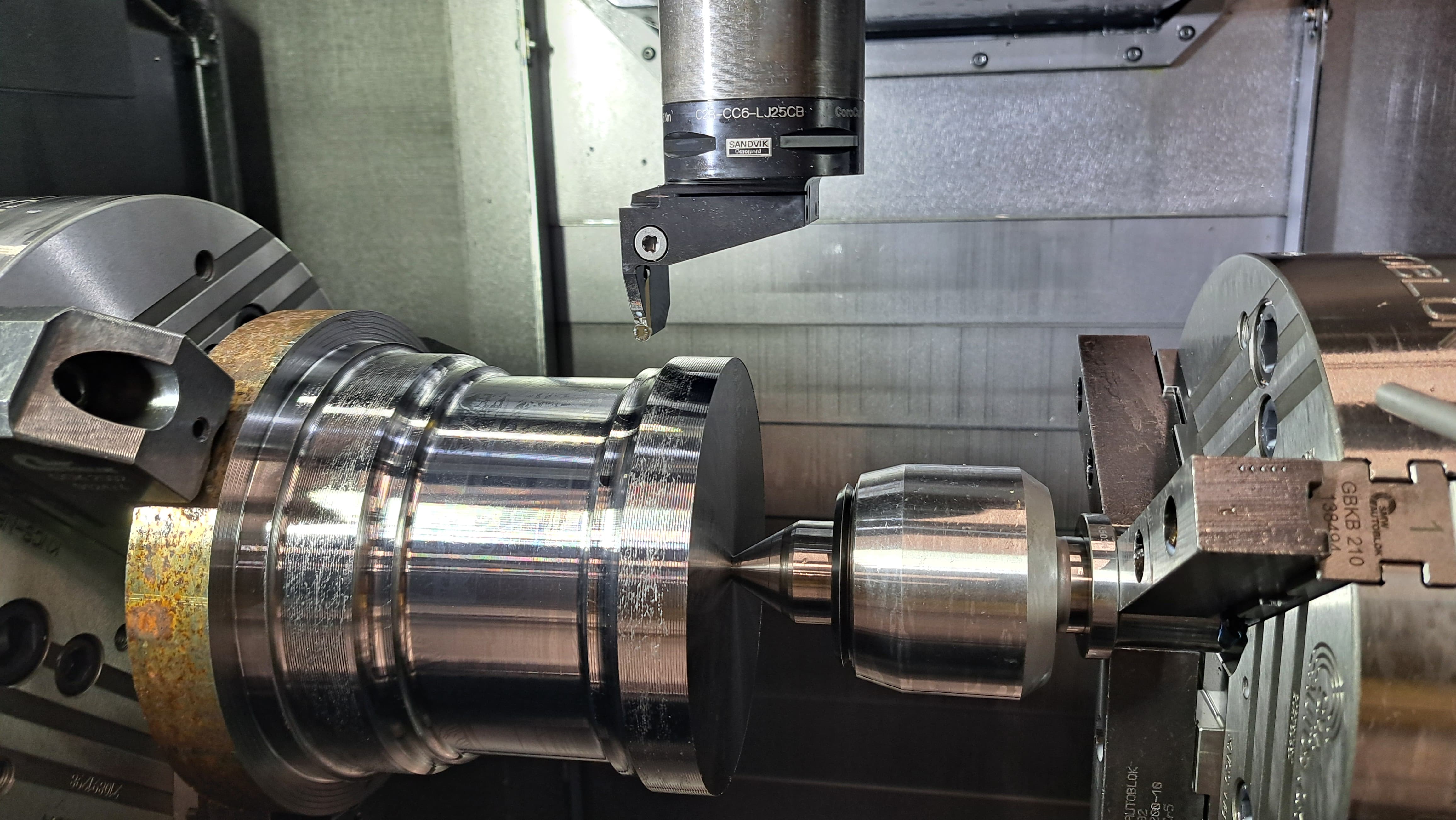
Learn how to implement data driven manufacturing in your factory today.
Manufacturers are starting to realise the need to use their manufacturing data to take action. Sometimes actually making that data available is the first problem.
Most machine tools sold today have some form of connectivity as an option or standard:
- Siemens has OPC-UA connectivity
- Mazak has MTConnect
- DMG MORI uses OPC-UA
- Haas uses Machine Data Collection (MDC)
We’ve explained how to collect data from your CNC machine here. It can cost a lot of time to connect each machine, and to get each connection working so your data is in a similar format. Each machine will present wildly different parameters and variables at different data rates. Imagine you’ve got two kettles and one lets you read temperature every millisecond, and the other lets you read whether it’s boiled or not. Trying to present these two datasets together in a coherent way is a difficult task.
But manufacturers, especially successful ones that have been producing for decades have an asset list of legacy and new equipment. How do you collect actionable data from machinery that was born even before the internet?
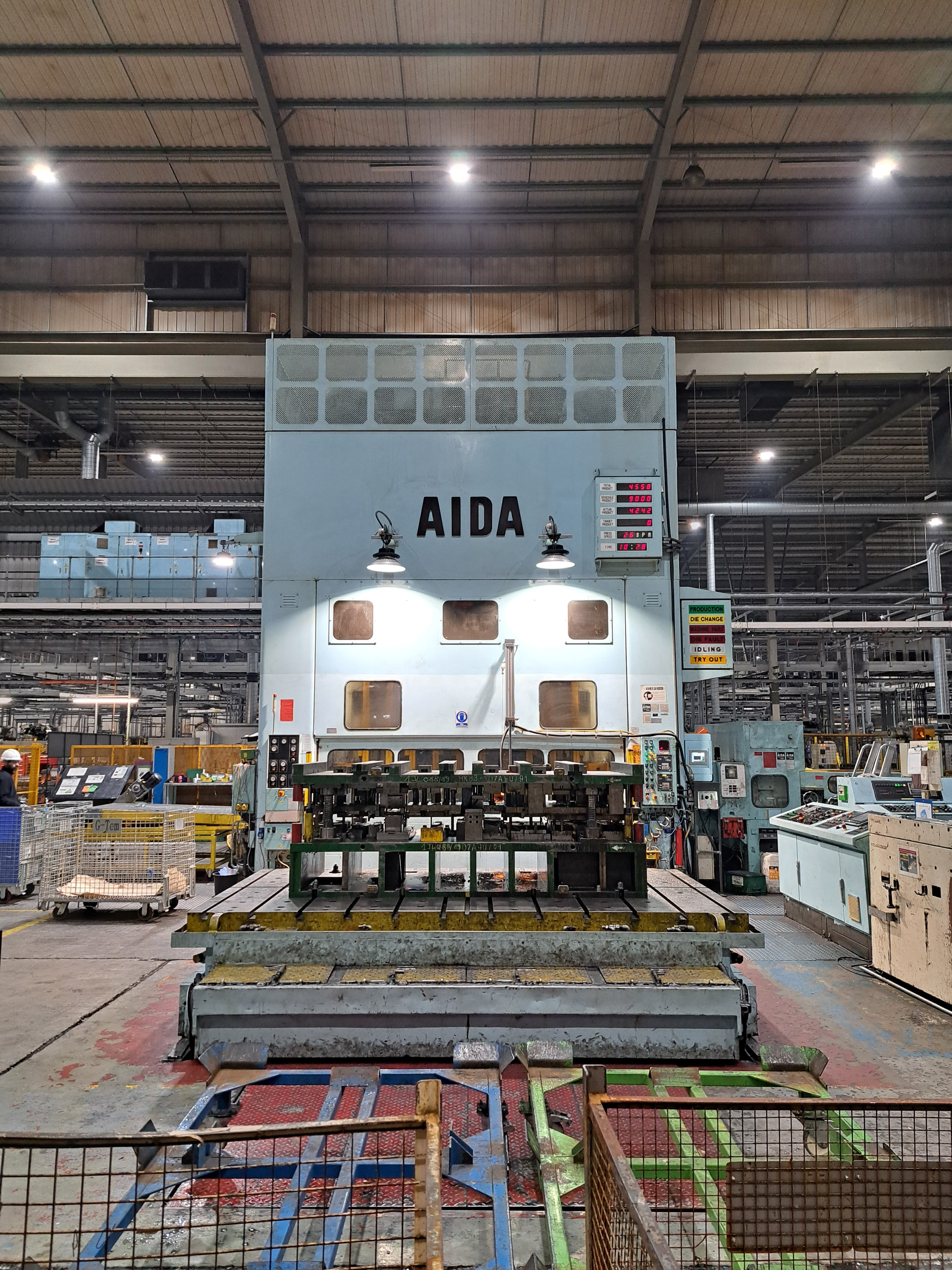
The most important thing to be able to do is understand your data. If half your machines aren’t connected, and the other half are giving different datapoints at different rates, it’s hard to find a consistent and understandable way to present how they’re running
Get better insights with the same data for every machine
Instead if you gather identical machine uptime data regardless of age or brand you suddenly have a foundation to work from. Now your machine uptime data is consistent, and you can start to look deeper and gain insights.
With the TMM Connect hardware you can gather machine uptime data using productive power data. If the machine draws power when it’s being productive then you can monitor its uptime. The hardware is supplied free and takes 5 minutes to install.
Go deeper into the data with powerful visualisation
With consistent data now captured without any intervention you can make insights into your data.
Product manufacturers
Product manufacturers might want to look at their lights-out efficiency. With TMM with your shift patterns set up, you can look straight at Out Of Shift machine uptime, or if you want to look at specific time ranges you can set up an extra shift called Lights Out and look just at that shift. Once you have a baseline uptime, you can make changes and implement steps towards lights out machining and watch your uptime in that shift grow.
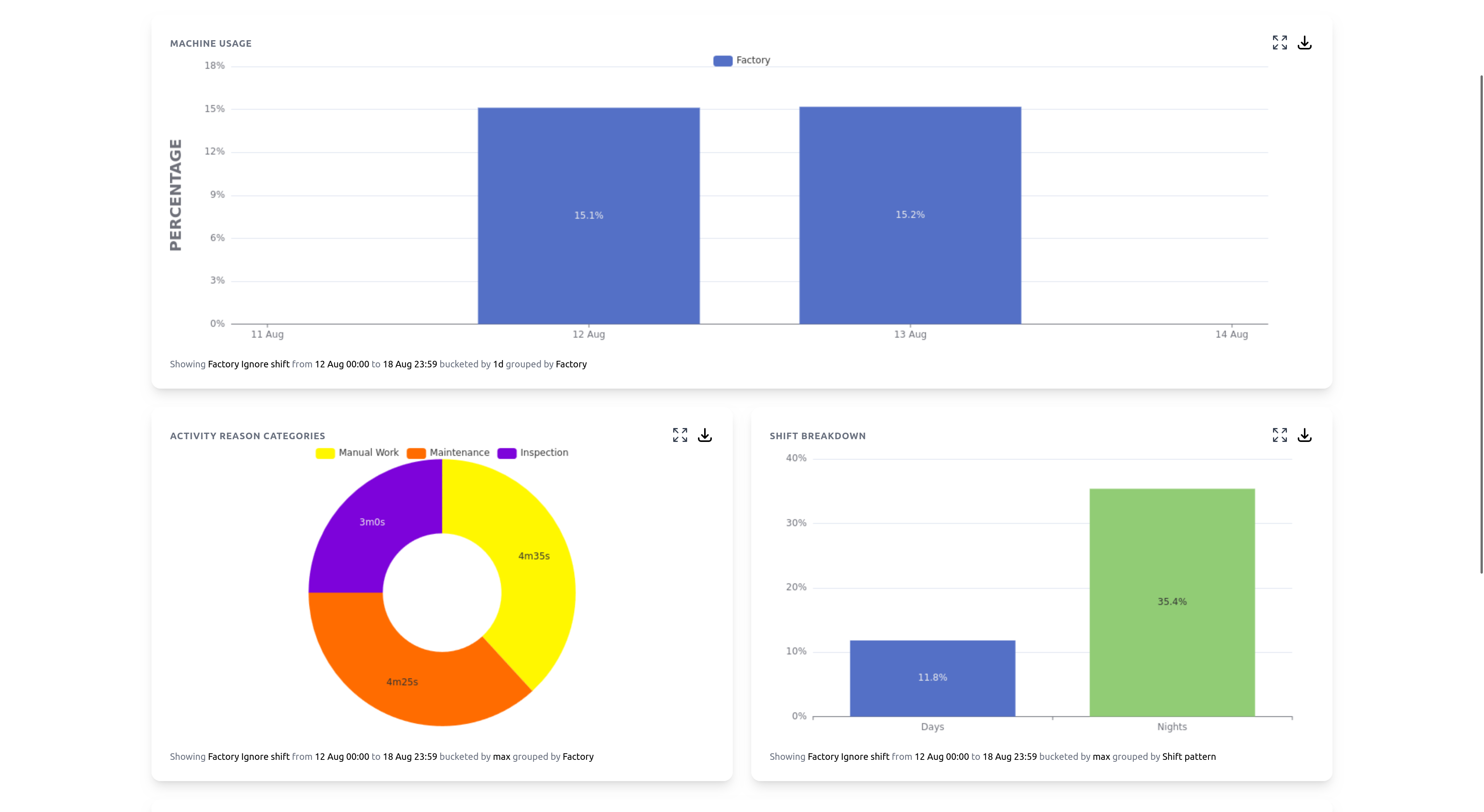
Subcontract manufacturers
With lots of different batches, these types of manufacturers might look at their changeover and setup times. With TMM you can run Work Orders, watch your Cycles and then measure your exact changeover times and set-up times with the Timeline.
Production line manufacturers
Manufacturers using more production line systems will want more information about each element in the line’s availability, and how the availability of one machine affects the others downstream in the line.
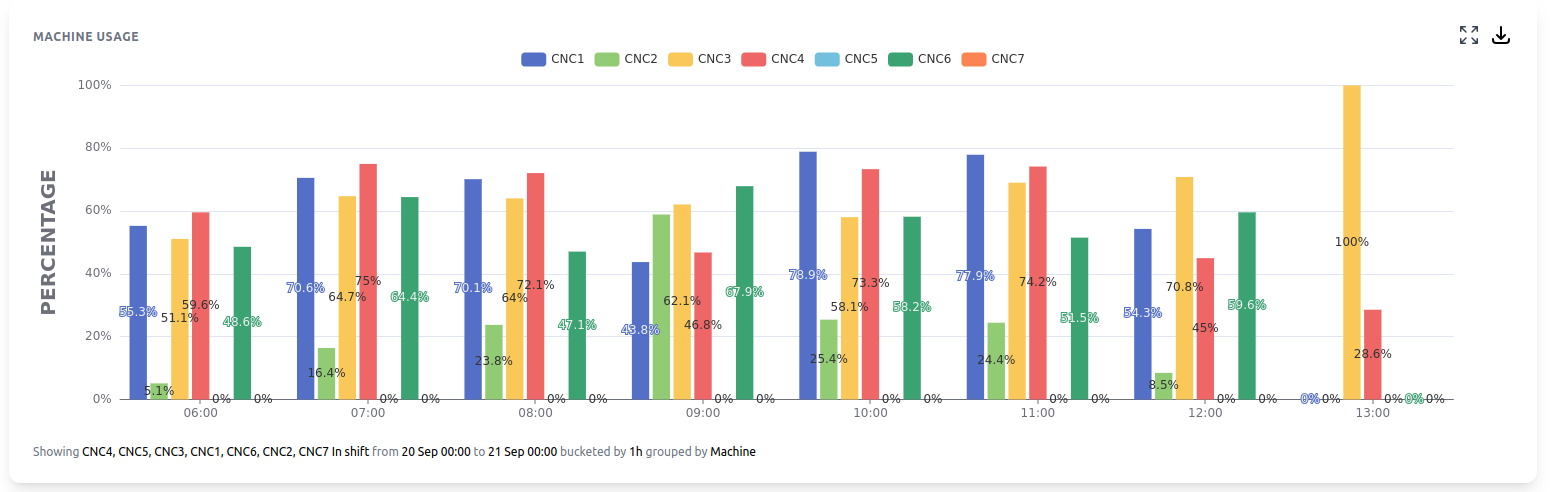
Benefits to data driven manufacturing
Once you start to find what metrics are relevant to your sector and type of product manufacture, there are two kinds of benefits.
Data will direct you to opportunities
When you can objectively measure the productivity of your machinery you can be directed to which elements of the production process need investment or revising. Sometimes it just takes a visualisation of an otherwise hidden process to confirm your initial intuition.
Being able to take machine downtime and put numbers against each reason also allows for a much easier justification for CapEx. Imagine the different between saying “We need better workholding because I think so” vs “We need better workholding because our changeovers will be reduced by 1h each say saving £528 per week over our two shifts”.
Data will measure your impact
You can use these metrics as baselines. Then once you start to implement changes you can measure how much time/money they’ve saved and how much they’ve increased productivity.