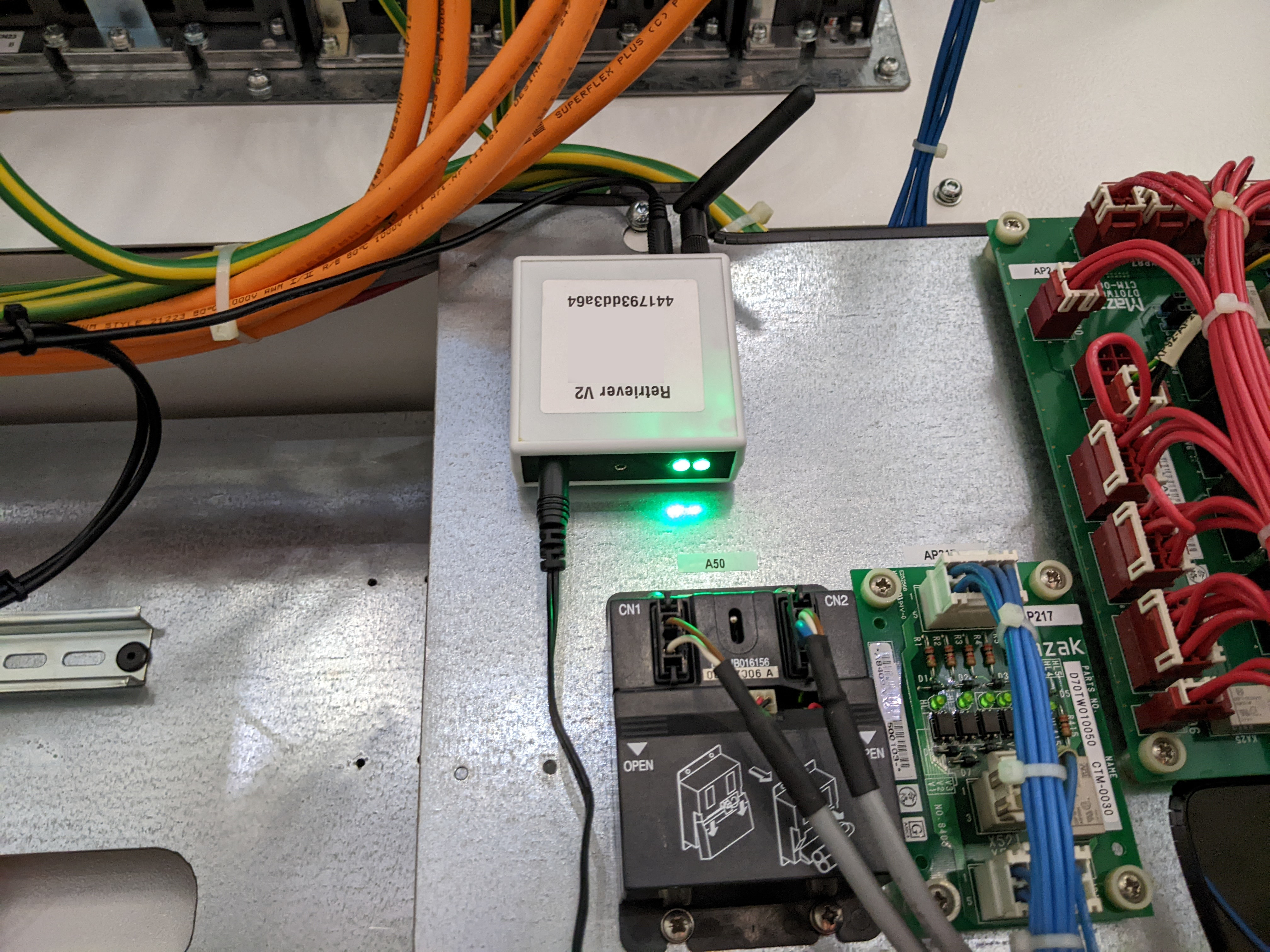
With electricity costs increasing it’s hugely important to measure your energy usage so you can try to reduce it. One way companies do this is by using their probably already installed distribution board. Modern boards will often have pulse counters with electronic displays. These give you an accurate measure of your single and 3-phase energy usage across your machine shop. You can note this display down to get a handle on what your daily usage of your factory is.
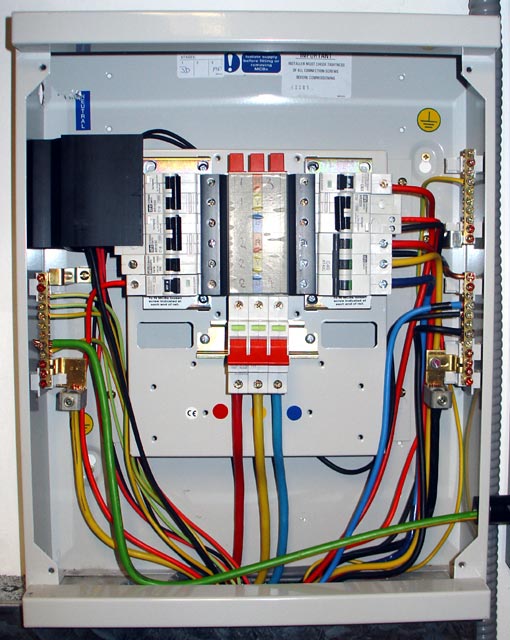
(Wikimedia Commons)
3-Phase UK distribution boardWith this information however, it’s not obvious where to target your efforts to reduce your consumption. Instead to do this you’ll need more granular information on what each machine in your factory consumes.
Energy, current, voltage and power
Before we talk about the monitoring hardware available for machinery, first we need to understand what energy monitoring actually is. Keeping it basic, your machine uses 3-phase electricity to run its motors, some pumps and high-power systems. It will also use single-phase electricity for its lower power auxilliary systems like the screen, LED lights and control panels.
The 3 phase or single phase energy used per second, or power P, is measured in Watts:
\[P (W) = Voltage_{phase} * Current_{phase} * Power Factor\]In this case, the RMS voltage and current are used as values for the voltage and current. For 3-phase power, the power in each line can be summed, as long as the voltage used is the phase voltage. The power factor is the value that accounts for the reactive load present in your factory, think anything with big windings like motors. The windings in these components are charged or “magnetised”, which uses some current that’s not converted into useful work.
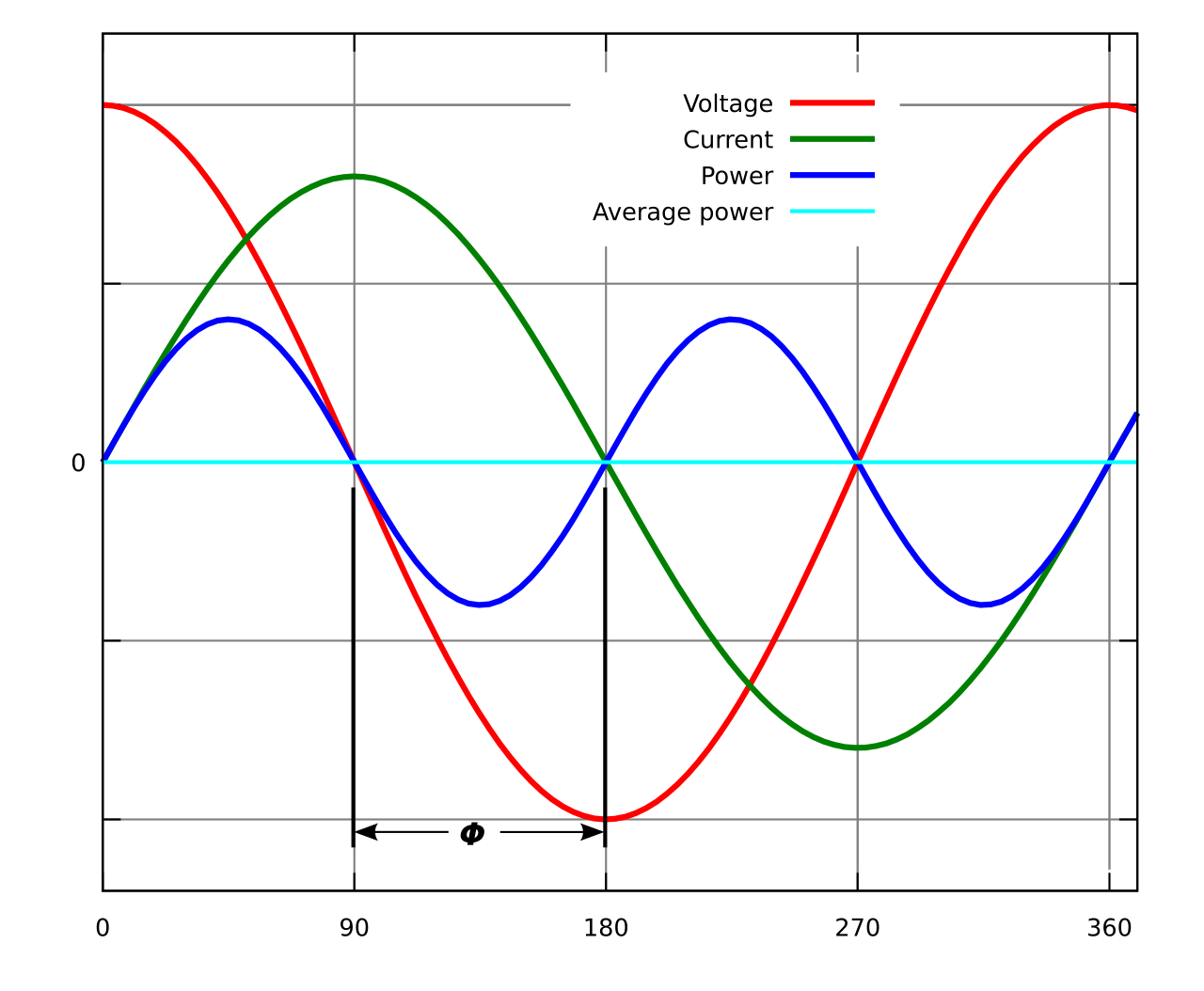
(By 121a0012 - self-made, after w:Image:ACPower03CJC.png by User:C J Cowie, Public Domain, https://commons.wikimedia.org/w/index.php?curid=2866717)
Power factor here at 90 degrees between voltage and current means measured or average power is zero, but the dark blue line shows real power is fluctuatingThe total energy E used over a time period can be measured in kilowatt-hours (kWh):
\[E (kWh) = P * Hours / 1000\]A usual figure for daily usage for a standard VMC machine for 8 hours is around 60kWh, costing around £14.40 per day. Per year this costs around £3600 at a UK price of 24p/kWh.
If you install measurement hardware on each of your 3-phase machinery it can start to cost more than your potential savings. That’s because the hardware must be installed invasively by an electrician and must accurately measure 3 voltage and current datapoints.
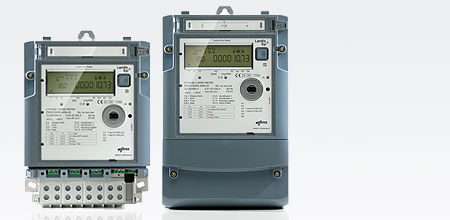
(Wikimedia Commons)
Energy monitoring hardware like this can be expensive to installInstead there’s another way to indicate what power your machine is drawing without calculating an exact figure.
TMM Machine monitoring hardware
Our machine monitoring hardware has been measuring machine current from a maximum of 3 sensors reliably. We have the system in place to offer this service with a quick and easy installation process. However, machine monitoring did not require current readings accurate enough for an energy usage calculation, so the hardware did not support it.
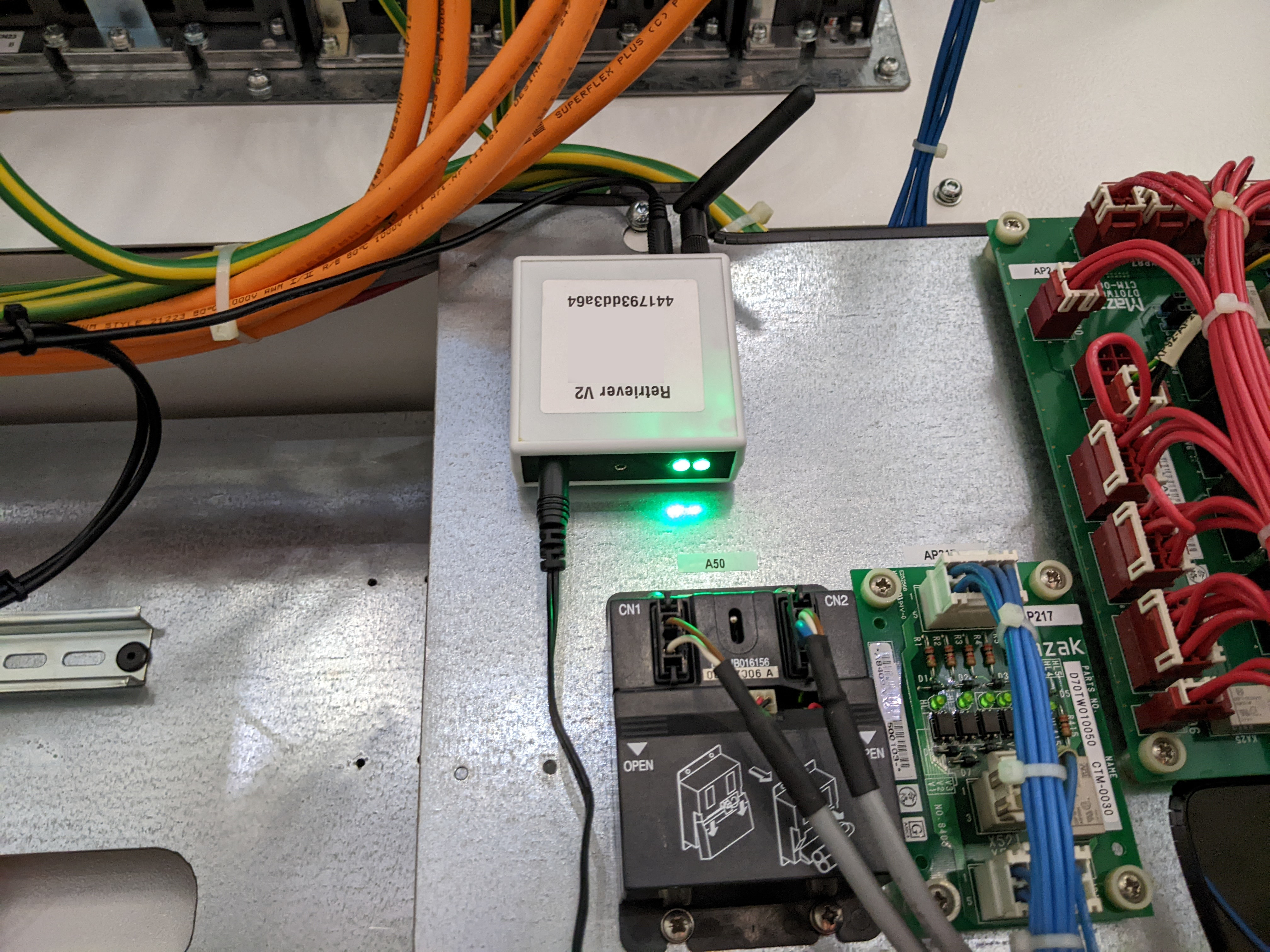
Now we can, with an extra input dedicated to energy monitoring we can measure the current going through a single phase accurately.
Obviously by measuring only current on a single phase we’re missing two components of the energy calculation for 3-phase equipment. This is fine for estimating the energy use of machinery for the purposes of saving money. Let’s dig into what this measurement is missing and how TMM accounts for it.
Estimate the voltage, assess the power factor
When we measure only the current running through the cable, we’re missing the voltage and power factor. We can assume the UK voltage for 3-phase is 415v. Obviously this will fluctuate within a tolerance, but will be enough to give an indicative reading.
The power factor is determined roughly by how many inductive loads are connected to the electrical system at one time. This value shouldn’t change as long as no new machinery, or old machinery is disconnected. By measuring the power factor once and adding it into the TMM system as a parameter, we can account for this value.
Single phase monitoring for 3-phase equipment
Once we’ve accounted for the lack of voltage and power factor, when trying to measure 3-phase energy we’re missing two of the three phases of the energy calculation.
Normally in a CNC machine one phase draws more power than the others since it’s also used for single phase auxiliary equipment. In this case we can measure this phase imbalance using the TMM hardware and account for it using a parameter.
Easy energy monitoring
It’s so important to make your factory as energy efficient as possible. Using a combination of technologies you can get both accurate cost savings and see where to focus your energy saving efforts.
You can use an accurate energy monitoring system like your distribution board for the whole factory. Then add a low cost non-invasive system like TMM to monitor not only the production of each machine but their energy use on an individual level.