
We’re already more than halfway through 2024, and our customers have been logging their downtime reasons to help spot the highest contributing factors to their machine downtime.
I’ve crunched the data for the first half of this year to show you what the top reasons for downtime across the TMM system is. Before we look at the results let’s look at why it’s important to measure machine downtime.

Why measure downtime?
Machine downtime contributes hugely to a component’s cost-to-produce. When machine’s aren’t running then the machine hourly rate is still counting up the actual cost of a batch, whilst the batch is making no progress in production. Most manufacturer’s don’t even measure the real runtime of their batches.
Understanding downtime reasons is key to production
The only way to reduce this cost-to-produce is to target those downtime reasons most responsible for machine downtime. That’s why TrackMyMachines allows operators to input their own reasons for downtime, so the highest contributing downtime reasons can be reduced, and parts can be produced in a shorter time for a lower cost.
Conclusions
Now onto the data! Taking all the downtime reasons logged from Jan 1st 2024 to June 30th here’s the chart (hover to enlarge):
The biggest culprit: Machine Breakdown! Taking over 20% of the downtime on TMM and costing over 655 hours, breakdown is a production-killer. In second place, closely following it, is Set Up at 17% of downtime and 557 hours of downtime.
If these two downtime reasons were eliminated. Over 1200 hours of downtime for the first half of this year would have been saved. Multiply that by your machine hourly rate and you can imagine the monetary value that represents.
For more in-depth analysis and recommendations for each of these downtime reasons, you can download the full report here:
Download the downtime reason report 2024 below
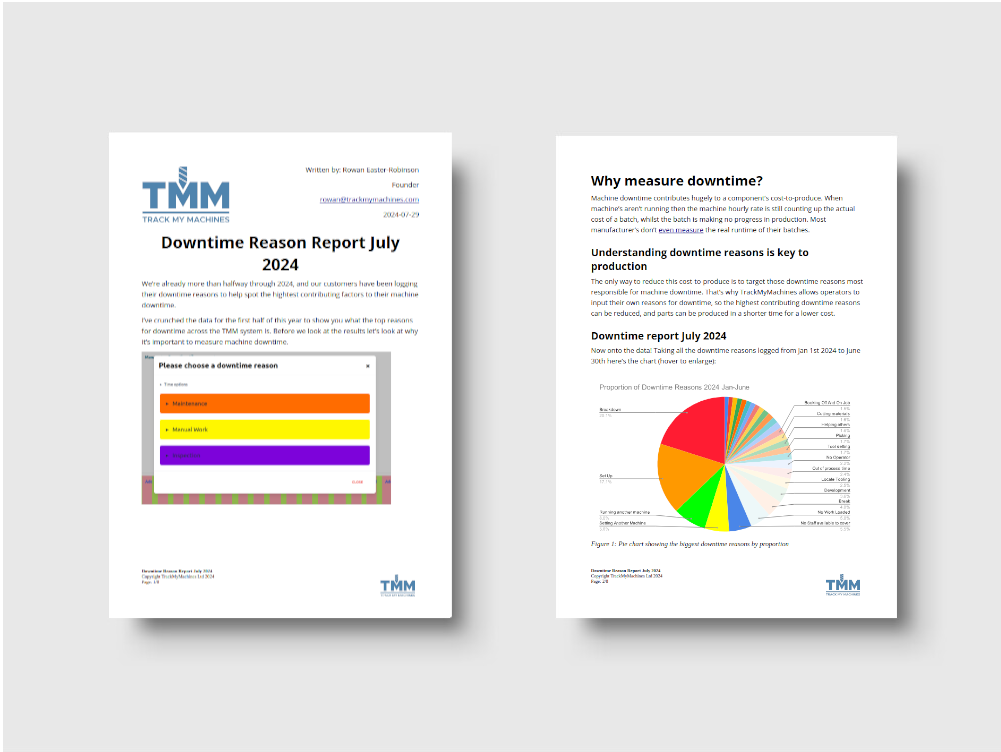