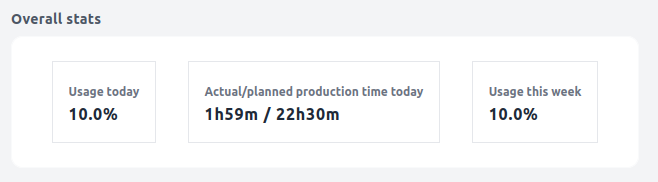
Why OEE might not be the right metric for CNC productivity
Saturday Jul 30, 2022
OEE (Definition) is a measure touted by a lot of manufacturing management experts. It supposedly combines three metrics into one single measure that represents your shop’s productivity. Like many simplifications however, this doesn’t fully capture the major differences between manufacturing methods. What works for a bottle-making facility won’t work for a CNC machine shop.
What is OEE?
First let’s find out exactly how OEE is calculated:
OEE = Availability * Performance * Quality
Where
- Availability = Actual uptime / Planned uptime
- Performance = Actual cycle time / Ideal cycle time
- Quality = Good parts / Total parts
Availability is really easy to calculate, either by hand or with machine monitoring. We even show it pride of place in our TrackMyMachines dashboard:
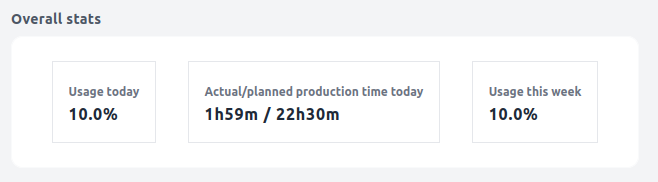
Quality is, again, easy to calculate. Once you’ve inspected your parts, you know the proportion that are good. There’s other statistical techniques if you’ve got a large and only want to inspect a certain subset of them.
Performance however is tricky, what’s the best possible cycle time for a given part? It’s as low as possible - right? Well if your only limiting factor is your cycle time, then it must be. But no machine shop only optimises for cycle time because there’s not always someone available all the time to changeover a part. Sometimes if a machine has a longer cycle time, you can save on tool wear, and an operator can run more machines.
It’s a little more complicated than just reducing cycle times.
What is an “ideal” cycle time anyway? If you’ve got a new part or manufacturing process there’s no way to know how long it’s going to take. The job of estimating this cycle time is often left to an extremely experienced individual, whose best guess might still be out by a factor of 2 or more. So the Performance portion of OEE isn’t realistically possible to calculate in many cases.
There’s another point here as well, if you’ve got a long running part that you set in the evening and leave to run overnight, you’re getting “free productivity” whether or not you optimise its cycle time.
It’s these 3 factors that, in my mind, make the Performance measure not only misleading but incorrect however it’s calculated. If this measure is wrong, then that affects 1/3 of your OEE calculation. I would suggest that trying to make improvements using a measure that’s 1/3 wrong is probably the wrong approach.
Where did OEE come from?
It’s obvious that focussing on an OEE measure doesn’t capture any of this operational complexity. That’s probably because its origins were in specialised plants with assembly lines. Factories that make products like bottles, pharmaceuticals or cars. These kinds of factories make much larger volumes predictably. CNC machine shops are in some sense the opposite, especially the shops who take different work in every day in small batches.
Take a more nuanced approach
Instead, a less rigid approach is needed that takes into account the business’s needs and its engineering capabilities. Rather than just observing a simplistic metric, try to follow the thread from [machine uptime][machine_up] on a certain part, to how much profit that part produced.
It’s the closing of the loop between expected machining time and actual machining time that’s going to supercharge your growth as a business.
Although this investigative work by hand is certainly possible, but can be really time-consuming. A automated machine monitoring system makes this information transparent and easy to build a clear picture of what’s happening on your shop floor.
If you’re interested in improving your machine shop productivity, get in touch with me by clicking the “Request a demo” button below, or send me an email at rowan@trackmymachines.com.