What is planned and unplanned downtime in Manufacturing?
Monday Mar 14, 2022
Running machines doesn’t always go smoothly. Any experienced CNC operator can tell you about all the different ways a machine can be disabled. From bad coolant to a broken spindle there’s tons of ways downtime can occur.
What’s important however, is separating and identifying your downtime reasons between planned and unplanned. This allows you to spot areas in both production and maintenance that you can improve on.
(If you want to measure your downtime, check out my article here)
Unplanned downtime should be for maintenance
Unplanned downtime is downtime that was not expected. This might be either from a surprise machine breakdown or machine crash, .
The Marshall Institute explain that many organisations run their machinery to failure. Regardless of it being a suboptimal approach, as machinery should be regularly serviced (check out Hardinge’s explanation of Preventative Maintenance for CNC machines here, it results in unplanned downtime when a machine breaks down.
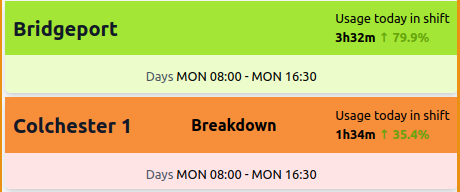
If other kinds of unexpected downtime (except from the results of run-to-failure) start to occur, such as production-oriented problems, then these must be investigated and eliminated. Unexpected production-oriented problem can and should be avoided. The way this is done is by the age-old methods of process proving.
How to reduce production-oriented downtime
Before a large batch of parts are made, the process must be proved, not just the program. The process is the system by which many parts are made - not just one. It’s a constantly changing environment. To avoid unplanned production problems, parameters such as tool wear, workholding repeatability must be measured across a multi-part run. It is this method that helps to define and then improve your Process Capability (cpk).
If you’re interested in the measurement and analysis of Process Cabaility - there’s a fantasic video here that explains the challenges with calculating your cpk for a machining process. There’s another breakdown of reasons into “common” and “assignable” causes that require an article in and of themselves. They’re explained generally here and also in the video above.
Planned downtime should be for everything else
Planned downtime is the downtime you were expecting to have. This could be anything from new product trials, tooling tests to planned machine servicing. Your aim is to get all your downtime into this category. How you do that is Process Control.
How to control your process
Process control is all about controlling variation. If variation is controlled and measured correctly, the process is said to be “in control”.
Let’s take tool setting as an example. If your operators set tools on-machine, then each operator will set them slightly differently, adding variation into the process.
If you were to use a tool presetter instead, the variation induced by each operator’s preferred tool setting method would be replaced by the smaller variation in the tool presetting equipment.
Applying this logic to all the sources of variation in your process will eventually result in only one source of variation left - tool wear. Then you’ve got total process control.